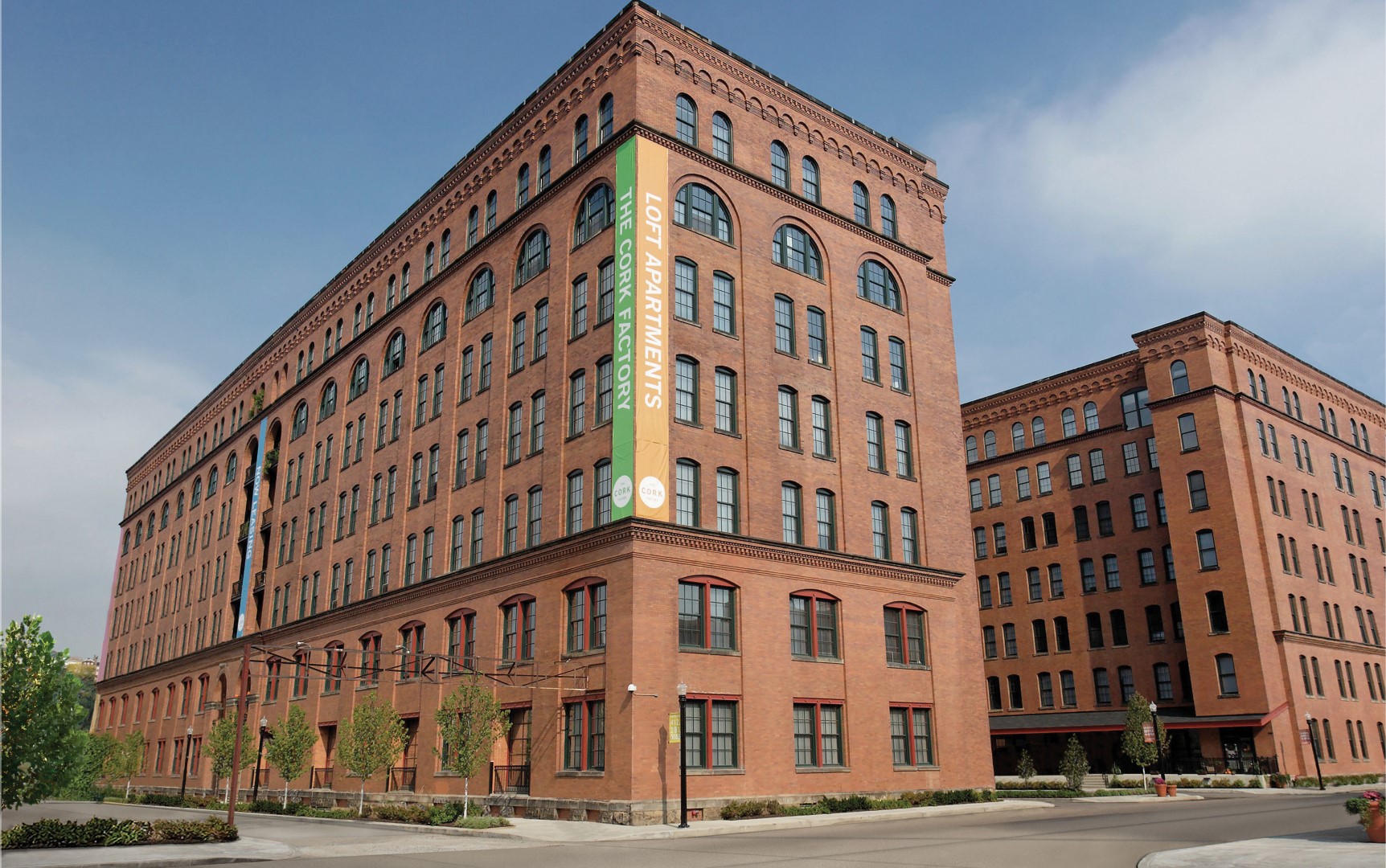
The Cork Factory is one of the most recognizable buildings in Pittsburgh, Pennsylvania’s Strip District. Designed by the renowned Pittsburgh architect, Frederick Osterling, the imposing Richardson Romanesque-style structures comprise the 440,000-square-foot complex that was constructed in 1901 and expanded in 1913. Home of the Armstrong Cork Company until 1974, the buildings were abandoned for more than 30 years. In early 2005, McCaffrey Interests, a Chicago developer, partnered with the local owners of the buildings to develop 295 luxury apartments within the shell of the former industrial facility.
Graciano Corp. was assigned the task of cleaning all of the two-building facility’s exterior brick masonry, stone and terra cotta surfaces. The company was also responsible for removing extensive accumulations of graffiti, as well as spot-pointing masonry joints, removing and replacing damaged brick, patching or replacing stone architectural features, and repairing damaged terra cotta trim on cornices, belt courses and window sills. Graciano encountered exceptionally heavy accumulations of dirt on the façade surfaces, and found it necessary to treat and clean exterior building surfaces two or three times to remove all foreign materials.
Midway through the assignment, Graciano was asked to assume interior work started by another contractor. This assignment required craftsmen to be quickly certified in lead abatement. Crews removed paint, dirt and graffiti, and executed masonry repairs. Graciano was then retained to stabilize exposed concrete ceilings throughout the complex. After masking off all finished surfaces, spalling concrete was removed from existing rebar, and the ceiling surfaces were repaired and refinished. The interior work concluded with the rebuilding of two elevator shafts to accommodate new equipment, as well as with the construction of numerous concrete block walls in the basement areas to create laundry, storage and mechanical spaces.
Graciano was subsequently asked to work on the complex’s towering stack. The company encapsulated the brick structure in scaffolding, reconstructed the top three feet of brickwork, replaced metal stabilizer rings, cleaned and repointed the masonry surfaces, and installed a stainless steel cap on the stack to prevent water infiltration.
When the stack work was complete, the company was then invited to work on the reception building. Two of the building’s three exterior brick walls were completely rebuilt to match the historic fabric of the surrounding structures. The third wall was refurbished with cleaning and pointing. Within the reception building, interior brick walls were constructed to define spaces. As a final assignment, the general contractor asked Graciano to install precast coping around the facility’s new in-ground pool and adjoining Jacuzzi.
Project Details
Downloads
Project Included
- Waterproofing
- Vertical & Overhead Patching
- Unit Stone Replacement
- Terra Cotta
- Structural Steel Repair/Replacement
- Stonework
- Stone Patching
- Stone Facade Pinning
- Sealants
- Sand Blasting
- Repointing Masonry
- Replacement
- Repair
- Parapet & Coping Reconstruction
- Paint Removal
- New Brick Construction
- Masonry Surface Rehabilitation
- Lintel Replacement
- Individual Brick Replacement
- Full Depth Concrete Repair
- Expoxy Injection
- Dutchman Repair
- Concrete Restoration
- Chemical Cleaning
- Brickwork
- Brick Facade Rebuild
- Abrasive Cleaning
Glossary Terms