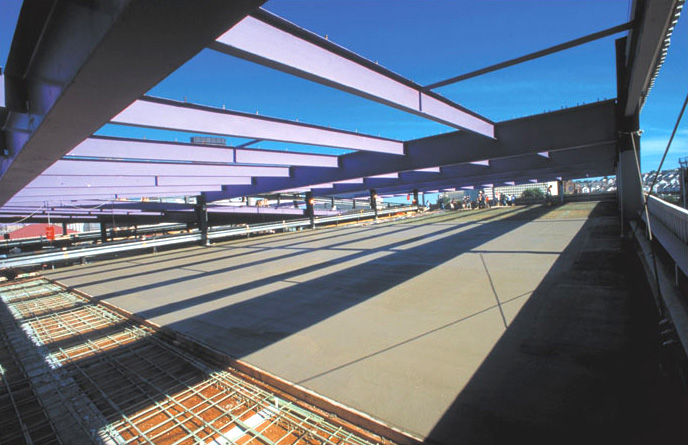
Twenty-five years of exposure to road salt, water and changing temperatures have taken their toll on the parking garage structure at the Mt. Sinai Hospital in New York City.
Graciano Corporation, the acknowledged leader in the care and restoration of buildings and structures, was selected to restore the 150,000 sq. ft. facility. Early structural evaluation exposed significant damage, including water and salt penetration and attack of the reinforcing steel rebar. It was also determined that rusting rebar had expanded, causing the concrete to crack and spall.
Tom A. Corbo, Vice President/General Manager of Graciano’s New York Office, managed the year-long $3.5 million project. Specialized, highly trained repair teams began with the restoration and removal of all six levels of the garage’s damaged concrete and supporting deck, leaving only the deck’s steel skeleton.
Graciano’s concrete repair craftsmen then repaired the remaining non-deck concrete which was cracked, spalled and broken. They installed new decking and reinforcements and replaced curbs. To weatherproof and seal the new garage surface, Graciano’s specialists applied an advanced urethane coating system and watertight sealants to make decks impervious to deterioration.
Project Details
Downloads
Project Included
- Waterproofing
- Water Control Injections
- Vertical & Overhead Patching
- Total Slab Reconstruction
- Structural Steel Repair/Replacement
- Sealants
- Reconstruct
- Pressure Washing
- Partial Depth Concrete Repair
- Full Depth Concrete Repair
- Flashings
- Expoxy Injection
- Deck Coatings
- Concrete Restoration
- Coatings
Glossary Terms